Supply chain leaders often focus on two facets to improve their business: productivity and quality. Whether you’re working on the raw material picking or distribution end of the supply chain, computer vision can help automate your continuous improvement projects, or “Kaizen” events.
I, Daniel Bender (author and recently hired Roboflower), had the privilege of working in supply chain contexts. I’m Lean Six Sigma trained and held roles in woodwork engineering and distribution management.
Below are three example computer vision applications that could serve manufacturers and distribution centers based on my experience at furniture and wood manufacturers. Each of these models are intended to be proof of concepts of what’s possible, although your specific data will likely require tailoring. I built these example use cases with Roboflow’s tools in under a day.
Use Case #1: Veneer Picking
This veneer picking model could be a potential use case to “Poka-Yoke,” or mistake-proof the veneer picking process for furniture manufacturers. Wood manufacturers often struggle to pick the correct veneer due to close similarities between certain veneers like Blond Ash and White Oak. If the wrong veneer is picked and sent further along the process without being noticed, all labor and materials have been wasted and the process starts over.
As a possible solution, wood manufacturers implement a classification model to detect which species of veneer is present when picking, eliminating the need for operators to guess which veneer they’re picking.
The model could be implemented at the veneer station where a sheet of veneer is placed under a camera, which then detects whether Oak, or Ash (or something else) veneer is picked. With this powerful application, manufacturers can effectively eliminate human error, and produce the correct veneer for the job, 100% of the time.
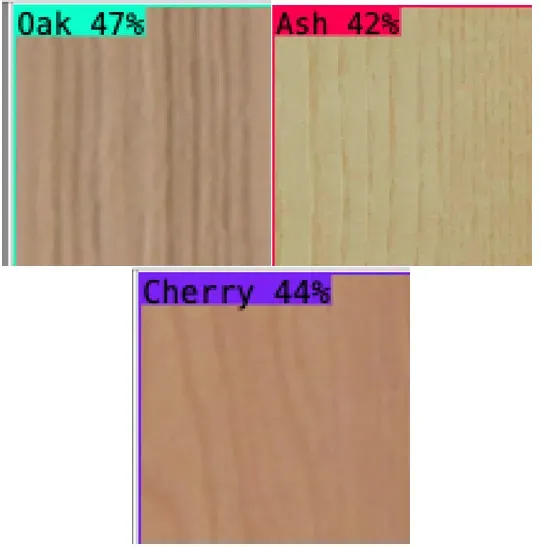
Use Case #2: Veneer Defect Detection
Veneer is a natural raw material, it’s susceptible to disfiguration. As the veneer is picked, it must also be scanned from top to bottom for defects, such as knots (see visual below). It does not end there; defects may arise as they are processed further. A strong quality system will implement an object detection model at the veneer picking stage as well as at the end of each process to account for operator error.
Similar to the last model, this object detection model identifies defects in the veneer once it’s picked. Common defects include knots, chatter, or mineral streaks, to name a few. This model can run in addition with the classification model.
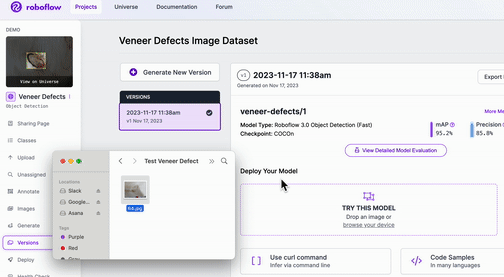
Use Case #3: Inventory Counting
The last model discussed applies to a distribution center (DC) setting. In a DC, operators will likely store, prepare, and ship vendor material. In short, a DC is a temporary “hub” for inventory to sit until it is destined to move forward in the supply chain.
Often, inventory is received in raw form from the vendor and must be processed to prepare to reach the end consumer. Inbound receiving operators unpackage inventory and scan each SKU into their inventory management systems. This is a tedious process for high-volume distributors. For example, a softline DC may unbox 200 tiny ballerina slippers in a single package! Having to scan each one is time consuming and hinders productivity.
What if we could scan the first SKU and leave the rest to computer vision? Here’s where the inventory object detection model applies. It detects both the parent barcode of inventory and a sample set of inventory. With a counter developed, this model can set-up at each receiving station and count each SKU so the operator doesn’t have to. Receiving throughput increases exponentially.
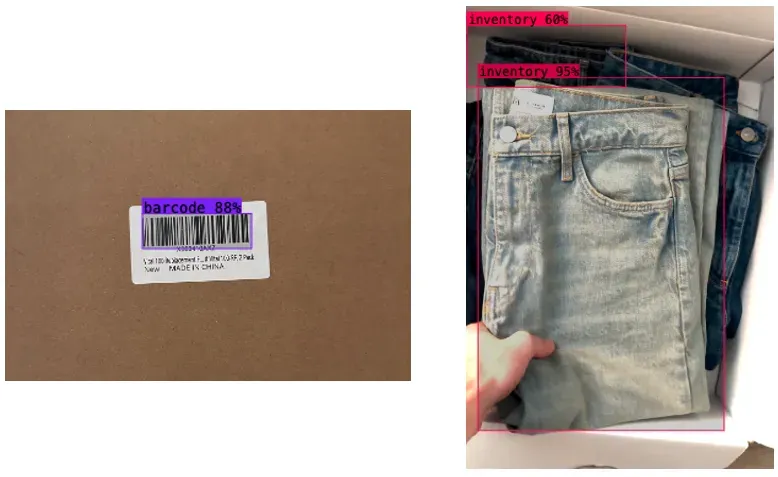
Conclusion
These applications are a small reflection of the endless opportunities with computer vision in manufacturing and quality assurance. The veneer identification model exhibits value by eliminating human error when pulling veneer for a batch, or job. The inventory counter exponentially increases productivity by automating SKU count, removing the need to scan every single SKU.
Lastly, the veneer defects model serves to catch poor quality at the point of failure, eliminating the wasted processing of the defected part further down the line. On Roboflow Universe, where these three projects are available, there are over 200,000 public datasets created and available to view and even utilize for one’s own applications.